Page 2 of 8
Posted: Tue Dec 04, 2007 2:01 pm
by jem
Kayak Jack wrote:My experience exactly. Looser weave accommodates curvilinear surfaces such as we routinely use in boats. (Pretty big word there, ehh? Aint'tcha proud of me?)
gold star for Jack.
Posted: Tue Dec 04, 2007 3:31 pm
by hairymick
Thanks for the tips guys. Pure gold!
I have never seen cloth quite like this before. It is perhaps, a little thicker than tissue paper and a very tight weave. I am thinking I may need to re- inforce/build up the high wear areas a bit.
Will post more shortly.
Posted: Tue Dec 04, 2007 5:33 pm
by hairymick
A few more thoughts.
What I tried on my Laker re applying the fibre-glass, was that I saturated the ply in epoxy and then waited till it was allmost touch dry. I could then work my cloth into place, slowly and carefully and it held there, in place, during wet out.
It worked a treat with my other cloth and was particularly helpful when doing the interior.
When I get to that stage, will post more detailed stuff and give my thoughts on the process and if it works.
Although I think there might be a few problems getting this cloth to conform, I am pretty excited at its light weight. It shouldn't be too resin hungry, yet still provide good strength.
Posted: Sat Dec 08, 2007 3:53 am
by hairymick
OK,
Some more thoughts,
I have some 6 oz stuff that I think I will use on the outside of the hull and keel the light cloth for the inside and decks etc.
Robin is very hard on the bottoms of her boats and the ply will probably need all the protection it can get. the extra weight won't be too much and will be well worth it I think.
Temp frames going in.
Starting to look like a boat.
Stitched and turned over. (I love this 4mm gaboon ply!)
Tacked up!
Pretty happy with my day"s work.
Oh yeah, I am trying not using spacers, just to compare.
Posted: Sun Dec 09, 2007 3:43 am
by hairymick
Stitches are out, exterior fillets cleaned up and final filler put in where the stitches were.
I am finding it much quicker and easier not using the spacers, though a little more care is required to achieve proper panel alignment. Also, I used much less woodflour in the process,
I found it helpful to brush some pure epoxy & hardener into the seams before applying the woodflour. This achieved a couple of desireable outcomes.
1, The ply absorbed the pure resin right through the joint even where the corners of the ply edges where hard up against each other.
2. With the ply allready saturated, there was less shrinkage in the woodflour.
3. An inch or so of dry resin on either side of the seam also made for easier/safer sanding of the ext. fillits without removing too much of the ply in the process.
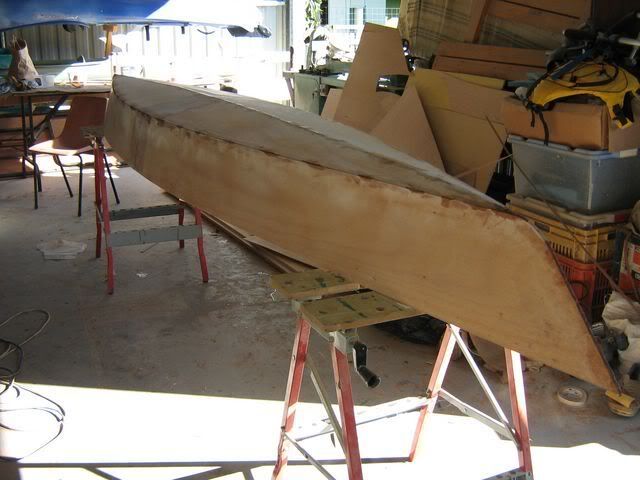
Posted: Wed Dec 12, 2007 12:46 am
by hairymick
My latest order of resin & hardener arrived today
26kgs
Hull is cleaned up and saturation coat is on.
I waited till the saturation coat was only just tacky before laying this up.
here we go.
This cloth is a little harder to get to conform with the shape of the hull, but not too bad.
First wet out coat.
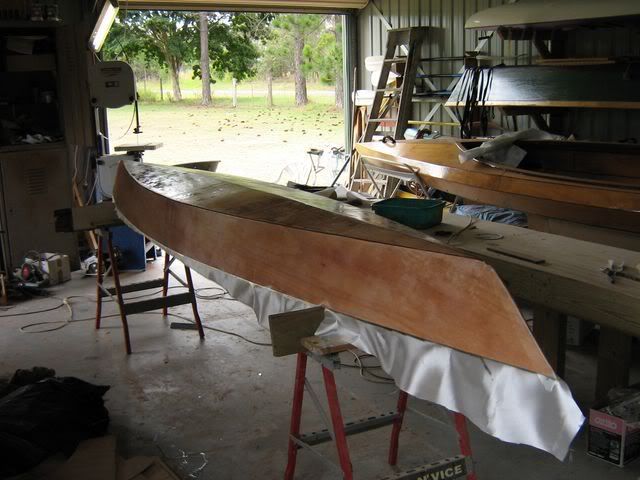
Posted: Wed Dec 12, 2007 12:53 am
by Kayak Jack
Mick, is that the tight weave cloth? I hope it remains conformed to the hull and doesn't wrinkle.
Oh, and you need another 20-30 boats in that shed.
Posted: Thu Dec 13, 2007 2:46 am
by hairymick
G'day Jack,
Yeah mate, tight weave. I decided to get used to it before attempting the inside.
Oh, and you need another 20-30 boats in that shed.
Workin on it mate, workin on it. I need another shed too.
Outside has all the fill coats on.
When it cures hard, a light sand and a top resin coat to finish her off.
Prep for inside fillets, I cut a roll of 2" masking tape (pretty badly) in half for this job. ya don't really need 2" of tape on either side of he fillet. I just put the wobbly side of the tape on the outside of the seam.
Didn't worry about masking the stems. They will never be seen anyway.
Seams filleted. For the first time,

I tried Matts recommended method of lightly brushing resin over the fillets when still tacky. Works a treat.
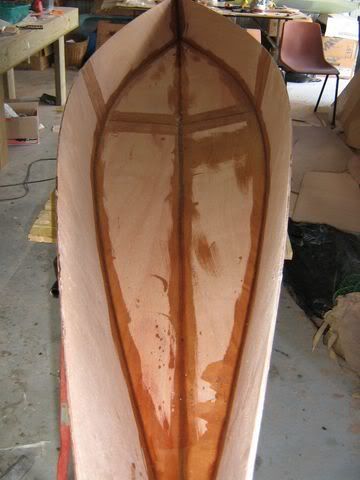
Posted: Thu Dec 13, 2007 2:57 am
by hairymick
Worked cloth off cuts into the wet stem fillets. I find it a lot easier to do it this way than to try to get a proper lamination when the stems are dry.
I had to wet out the tight weave cloth for the inside in sections. It was way too hard for me to do it all in one go.
While that was setting up, I ripped some 3/4" hoop pine into 1/4" strips, scarfed them where needed and then glued them in place for the sheer clamps. Wet on wet is a very good thing.

easy.
Back to work tomorrow so won't be getting much done for a couple of days.

Posted: Thu Dec 13, 2007 6:28 am
by Kayak Jack
Mick wrote: "...Seams filleted. For the first time, Embarrassed I tried Matt's recommended method of lightly brushing resin over the fillets when still tacky. Works a treat"
'Splain yousef, Lucy. Can you give more detail on this? I'm curious.
I like the idea of rooting the inside glass into wet filets. More continuity that way. And I'm glad to hear you cut the tight weave into strips on the interior. I think that would have relieved much of the internal stress from the glass sheets had I done that. Did you run your sheets lengthwise or crosswise? More thoughts?